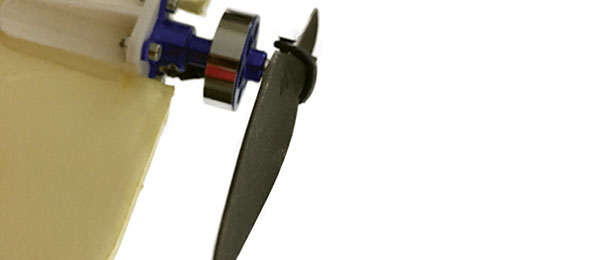
Written by Lucas Weakley New Technology Column As seen in the Spring 2018 issue of Park Pilot.
>> When I first began designing my own RC airplanes, determining the size of the propeller was probably the most confusing thing that I had to learn. Over time, I began to intuit which propeller to use. I’ll share how I learned this and show my process for selecting a propeller for an airplane design. A good place to start is propeller theory. Wait! Don’t leave yet! I promise I won’t get too technical; I just think it’s important to know why propellers are classified the way that they are. Propellers are classified by a set of two numbers. For example: 6 x 4, 8 x 3.8, or 10 x 5. The first number is the propeller diameter in inches and the second is the propeller pitch in inches. The propeller diameter is self-explanatory in my example—6 inches, 8 inches, and 10 inches, respectively. The pitch is where things become confusing. Pitch is usually an angle measurement, but now it’s a distance. Here’s why. A propeller is a spinning, twisted airfoil. This twist in the airfoil allows for even force distribution across the entire propeller blade. The pitch angle at the blade’s tip is shallower than the steep pitch that is closer to the hub because the tip is spinning much faster than the hub, and therefore doesn’t need to “bite” the air as much to create the same thrust. The twist also means that the pitch angle is not constant over the span of the propeller blade. Therefore, we can’t rely on pitch angle for propeller classification. So now what do we do? Well, we look at pitch distance. Imagine a screw being driven into a piece of wood. The screw teeth have an angle, and when we turn the screw 360°, it goes into the wood a certain distance, which is constant. A propeller does the same thing.
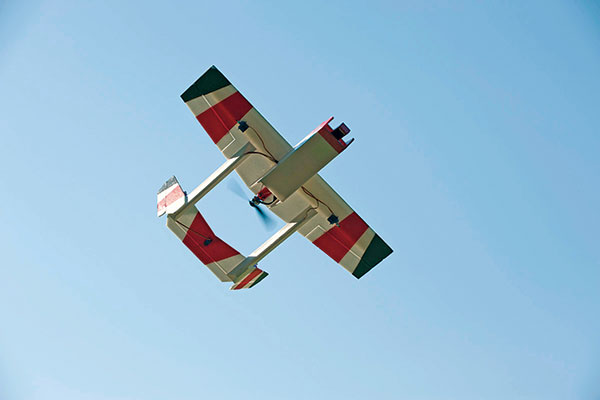
The Maker Trainer 2 has a 30-inch wingspan and an 8-inch propeller. This makes the propeller slightly more than 25% of the overall wingspan, so the airplane rolls from the torque on takeoff. Photo by Kent Weakley.
Imagine spinning a propeller in a thick fluid. If it never slipped, it would follow the path carved out by the angle of its blades. In this theoretical case, the distance a propeller would move forward in one revolution is the pitch distance. So, for my example, it would be 4 inches, 3.8 inches, and 5 inches, respectively. That’s it! The percentage of difference between this theoretical pitch distance and the actual pitch distance of the propeller in flight is known as propeller efficiency, but now I’m getting too technical. In my aerospace engineering classes, when we design a full-scale airplane, we determine which propeller we’re going to use through a number of fancy calculations. Luckily, we don’t have to go this crazy in-depth for an RC airplane, although it is fun to know that all of the same equations apply to either case. There are several ways that you could go about selecting a propeller for your RC airplane. The first, and most obvious, is by looking in the product description of the motor you purchased. There will usually be at least a manufacturer’s suggested propeller diameter and pitch. Sometimes you’ll get lucky and the shop owner has done testing and can give you a list of propellers and the static thrust that they create.
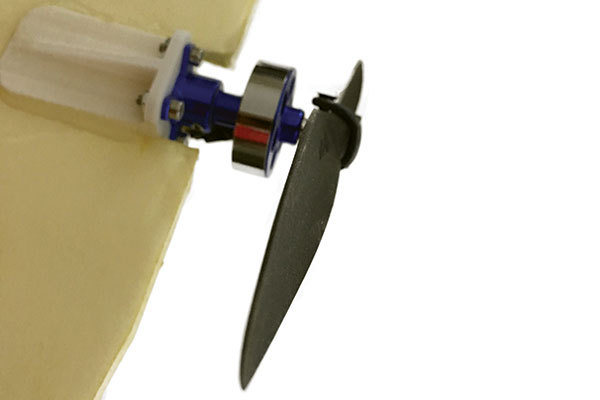
Looking down the end of a propeller, the twist that Lucas Weakley discusses can be seen.
This is how I do 90% of my propeller selecting, although you probably knew all of this already (if not, I just blew your mind!). What do you do when you have an airplane without a motor yet or one that you can’t identify? Now that’s more interesting! There are a few leading questions that you can ask about your airplane to derive which propeller size you should use. First, how does the airplane fly? Propellers are like the gears on a bike or a car. Large-diameter propellers have their greatest thrust at close to zero airspeed, and eventually lose the ability to create more thrust when the airspeed of the airplane exceeds the pitch distance rate of the propeller. Small-diameter propellers have low static thrust and produce the most thrust when they are operating at higher airspeeds. Because smaller propellers usually have much higher proportional pitches, they are also able to continue accelerating the airplane into much higher airspeeds. So, if the aircraft is meant to fly slowly, it should have a larger-diameter propeller and vice versa. To finalize the propeller diameter, look at the airplane’s wingspan. If the propeller is too large, the torque and gyroscopic effects coming from it will cause adverse flight characteristics that we don’t want. It’s generally a good idea to keep the propeller at approximately 25% of the overall wingspan. This can be difficult to follow, for example, when you have a 6 x 4 propeller for your 18-inch wingspan park flyer jet. These are just rules of thumb. On a slow-flying airplane, the wings won’t have enough air going over them to counter the torque, but the park flyer jet in this example will be going fast enough that the torque won’t really have an effect at cruising speed. Taking off with that park flyer jet will be sketchy because you will probably need nearly full throttle to get enough thrust to take off, and there won’t yet be air over the wings to counter the torque. You might want to have a friend help you launch.
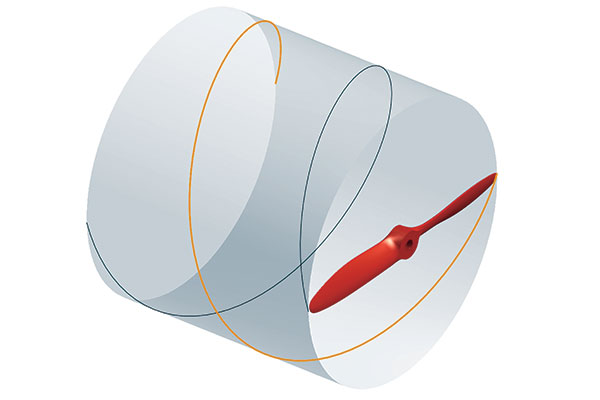
Here, the spirals follow the motion of the propeller through one revolution and the cylinder shows the pitch distance traveled by the propeller.
Pitch can be determined by looking at the current draw and Kv of your motor. The more amps that your motor and ESC can handle, the steeper the propeller pitch you can use. If your motor is rated at only 12 amps and has a low Kv (below 1,500), it should have a large diameter and shallow pitch propeller such as a 10 x 4. If your motor is rated at 40 amps and it has a high Kv (more than 1,500), the motor can likely handle a small, steep-pitched propeller such as a 6 x 5 or even a 7 x 4. Knowing when to use a propeller with more than two blades is just as simple. A three- or four-blade propeller will produce more thrust (while also being less efficient) than a two-blade propeller of the same diameter. They are used when more thrust is needed, but the diameter can’t be increased. This is why they are popular on racing quadcopters. Speaking of selecting propellers for multirotors, it is probably best to review propeller test data or do your own testing. Multirotors operate differently from airplanes because they mostly use static thrust to stay aloft. This means the intuiting way of determining your propeller that I explained doesn’t work for quadcopters. A big reason why manufacturers often include propeller test data with their motors is to cater to this market of VTOL (vertical takeoff and landing) aircraft. One last thing. There is a handy calculator for propeller sizes that you can use called WebOcalc (archive.is/IDDdd). It will give you a list of suggested propellers based on several aircraft parameters. This version does, however, require the use of metric units. Anyway, that’s how I’ve been figuring out my motor/propeller combinations for several years. I hope you’ve found some of the information here useful for your future projects! Although you could get much more technical with analyzing the efficiencies between using a 10 x 4 or a 10 x 3.8 propeller, take it from this aerospace engineer in training—for park pilots, that isn’t really necessary. -Lucas Weakley [email protected]
Article: