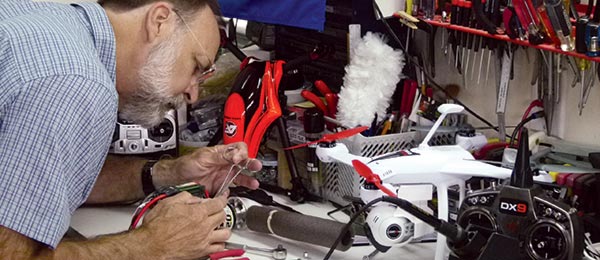
Written by Greg Gimlick Overcoming common issues Technical As seen in the Summer 2015 issue of Park Pilot.
>> In the world of electric flight, there are many things connected to make our aircraft fly and operate the way they are supposed to. Any time there are manufactured items making up an assembly, there can be malfunctions and defective pieces, but sometimes we’re the ones who are actually to blame! Sometimes it’s from rushing, sometimes it’s from ignorance (and by that I mean actually not knowing how to do things), and sometimes it’s just because we look beyond the obvious and don’t see the elephant staring back at us. Fear not. We’ve all been there. If you stay in this hobby long enough to become an expert, you’ll still make those mistakes. The purpose here is to open your eyes to some of the common things that happen that we often overlook.
ESCs
ESCs are little miracles of electronics that are the source of a lot of our problems, usually because we’ve done something wrong. Suggesting that you read the manual seems silly, but I can tell you from experience that it’s the main cause of “problems.” I know, because I’m as guilty as the next person of skipping over the manual or at least blowing through it so quickly that I miss important information. Here are some of the questions I’ve been asked, along with the answers. I plugged in the battery, but there are no sounds. This is usually because someone didn’t plug the motor into the ESC, or unplugged it on the bench for safety and didn’t reconnect it. The motor is the sound generator for the ESC and if it’s not plugged in, there is no sound. Be sure that all three wires are plugged into the ESC. Remove the propeller while you’re setting up your model. That way it will be safe and the motor can be checked and produce sound. I’m getting the initial tones, but it won’t completely arm. This problem can have a few different causes and each is usually related to some safety feature of the ESC. Manufacturers have different ways of doing things. Sometimes it’s to make some feature proprietary and sometimes it’s simply a different thought process on the engineering side. Regardless of the motive, you must read the manual to see the correct sequence for arming an ESC.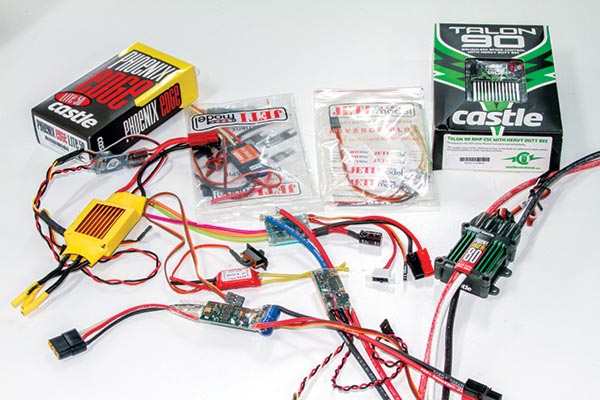
There are many ESCs on the market and they don’t all use the same arming sequence. Read your manuals!
The primary reason I see for this second round of tones not coming is that the ESC requires the user to show it both ends of the throttle range. This means that if you get the initial tone, you also need to advance to full throttle and wait for the second tone. When that happens, reduce the throttle to zero and wait for the final series of tones signaling a fully armed ESC. Remember, the propeller should be removed. If it isn’t, be sure to restrain your aircraft during this sequence, just in case. Another common cause is the throttle trim not being reduced to its lowest level or the throttle range not being set “wide enough” for the ESC’s expectations. If reducing the throttle trim to low doesn’t start the arming sequence, check the transmitter programming and set the throttle travel to its maximum, usually plus or minus 125%. The third most common cause is connecting a battery that is discharged. It’s easy to do at the field, so don’t laugh … if it hasn’t happened to you yet, it probably will. Find a way to keep the discharged batteries separate from the charged batteries at the field, or check the pack with a meter before heading to the flightline. I finally got it to arm, but it’s backward. This generally happens to those of us who own more than one brand of radio. Some require the throttle channel to be reversed before connecting it to an ESC. My Futaba, Tactic, and Tower Hobbies transmitters all require this. Check your ESC manual and the radio manual to see if this is the case for your brand of transmitter. What happens is that you don’t get the first tone, so you mess with the throttle and notice that you get it when you go to full throttle. Your next thought is to reduce the throttle and you suddenly hear the next tone. Hopefully this is when you realize what’s going on. If you don’t, and you advance the throttle again, you’ll hear the final arming tones. This usually startles people and they realize the throttle shouldn’t be where it is and quickly reduce it, causing the motor to come to life with full throttle because it was armed backward. The ESC thinks high is low and low is high. This is dangerous! Read the manual. If you own multiple brands, be extra careful to notice which one you are using at the time you go to arm the airplane.
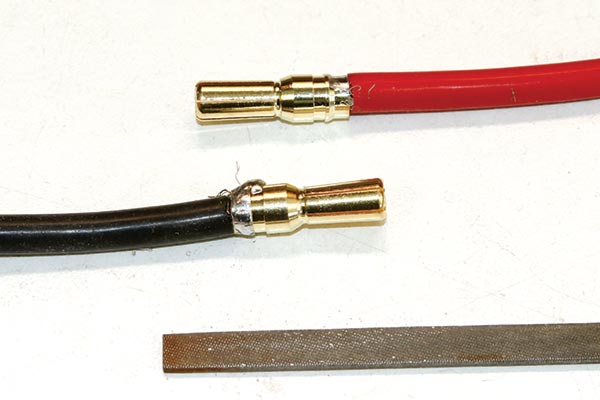
This bottom contact won’t fully lock into the EC5 connector housing because of the messy solder job. This must be cleaned up so it will lock into the housing.
Everything is armed, but the propeller turns backward and there isn’t a way to reverse it. This is way more common than you think, but the remedy is simple. Simply switch any two wires from the ESC to the motor. It doesn’t matter which ones; doing so will reverse the motor. It worked before and doesn’t now! Our systems are works of genius, but sometimes they still lose their “bind” or “link” to the transmitter. It’s not supposed to happen, but it does, and it does so without regard to brand or good reason. If your ESC isn’t arming, have you checked your other controls and verified that your receiver shows the LED signal for being bound or linked? If not, relink or rebind your system and try again. Do you have the correct aircraft selected in the transmitter? Some radios won’t let you fly with the wrong airplane selected. If you have more than one transmitter, are you using the correct one?
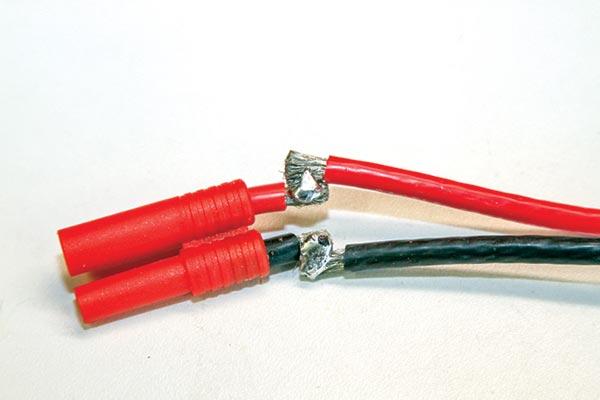
This is just all bad! Sloppy solder work, a cold joint, and being improperly tinned before joining. Never accept sloppy work such as this.
Battery-Related Issues
It charges just fine, but dies on takeoff. If you know it’s charged and it dies on takeoff, it’s usually because the battery has developed an internal problem you can’t fix. There is probably a cell within the pack that is dying (or the internal resistance has increased significantly compared to the others). These often appear to be normal with a 1C charge, but when a load is applied (such as takeoff power), the voltage of the pack sags instantly and the ESC’s low-voltage cutoff kicks in. The result is a deadstick at the worst possible time. What can you do to prevent it? Keep a close eye on the flight times you get with a pack and note when they begin to significantly drop. This indicates a growing problem. There are battery testers that will load a pack to real-life current levels, but most of us don’t have anything that sophisticated.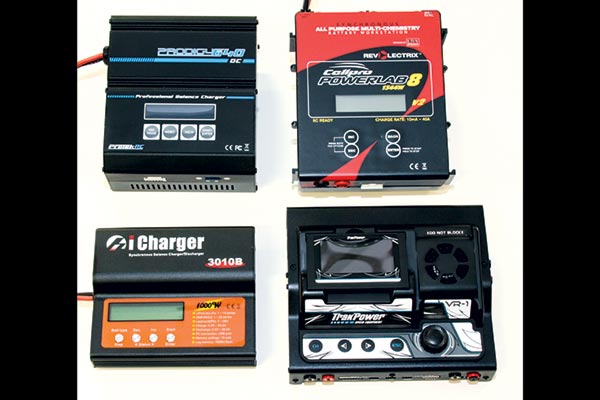
These chargers will do more than charge. They can check internal resistance and give you a heads-up before a pack goes south.
The pack is good, but it only seems to work intermittently in the airplane. This can usually be traced to a connector issue. I love APP (Anderson Power Poles), but if the contact inside the connector body isn’t fully seated and locked with the internal tab, it can slide backward during the connection. This happened to me when everything seemed fine. The aircraft armed and taxied out to the runway. I advanced the throttle to take off. As it rumbled and bounced down the grass field, the motor cut off. When it stopped, nothing appeared wrong, so I tried it again and had the same result. Close inspection in the pits found the tab inside the housing didn’t lock one of the contacts. Bouncing down the field caused it to break the connection. When it was still, it rested enough on the other side to make the connection. It was fine unless there was movement. I apparently didn’t assemble the connector correctly. I stopped pushing the contact in before I got an audible click. Other connector types can also give intermittent service if they aren’t fully pushed together and seated. A soldered connector might have a stress fracture in the solder joint. Sometimes solder wicks up the wire and will cause a break inside the insulation. Troubleshooting isn’t difficult. The first step is to jiggle the connector and see if things change. Visually look for anything that isn’t fully seated or is possibly corroded. Pushing, pulling, jiggling, vibrating, and visual inspections are all common-sense troubleshooting methods.
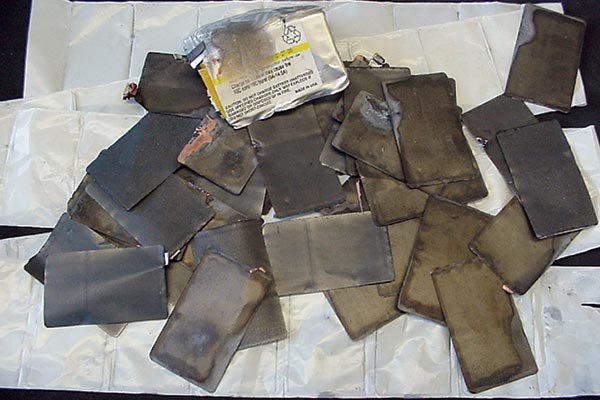
This is the inside of a LiPo battery. Never disassemble one! This was done in a lab by an expert for demonstration purposes only.
The Bottom Line
Problems happen to everyone! Most of the time our issues stem from easy things, but we look past them. If you run into a problem, follow these simple steps: 1. Stop and step back. 2. Think about everything you did. 3. Look for the obvious. 4. Start over after you’ve ensured it’s all properly connected. 5. Know your manual. 6. Follow your arming sequence and pay attention to each step. 7. Don’t allow yourself to be distracted. 8. Remember, it happens to all of us. -Greg Gimlick [email protected]Article: